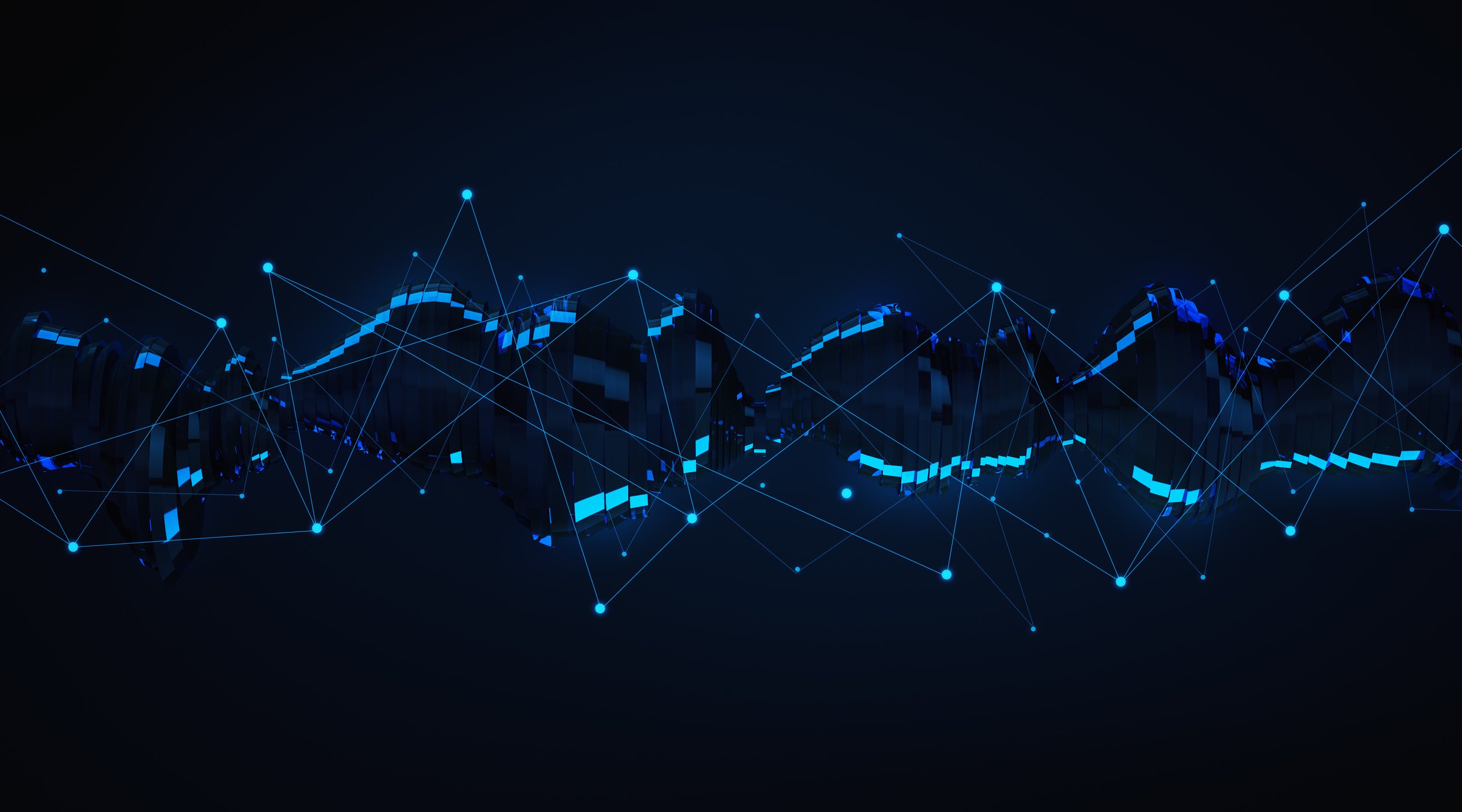
AMCOSTAR is a new Eurostars/Eureka Network and Innovation Fund Denmark funded Eurostars project on Adaptive Control of Airkeel vessel stabilizer systems.
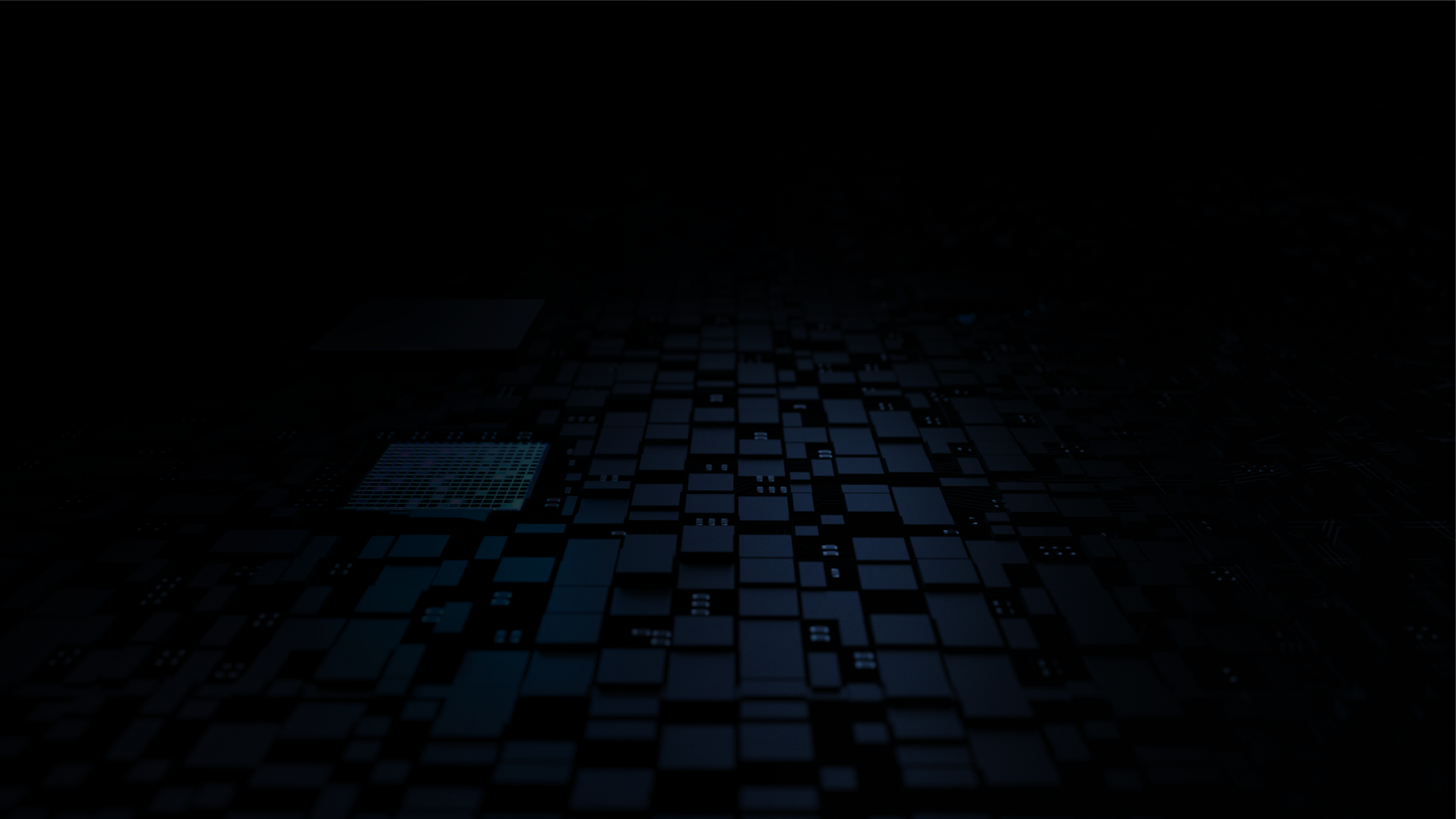
Project news
📣 AMCOSTAR news: Papers accepted for presentation at the prestigious #IEEE CCTA 2023 Conference and the #IEEE CDC 2023 Conference regarding investigations made by SDU for marine vessels equipped with the #Dacoma Airkeel.
The full papers will be available shortly in IEEE Explore.
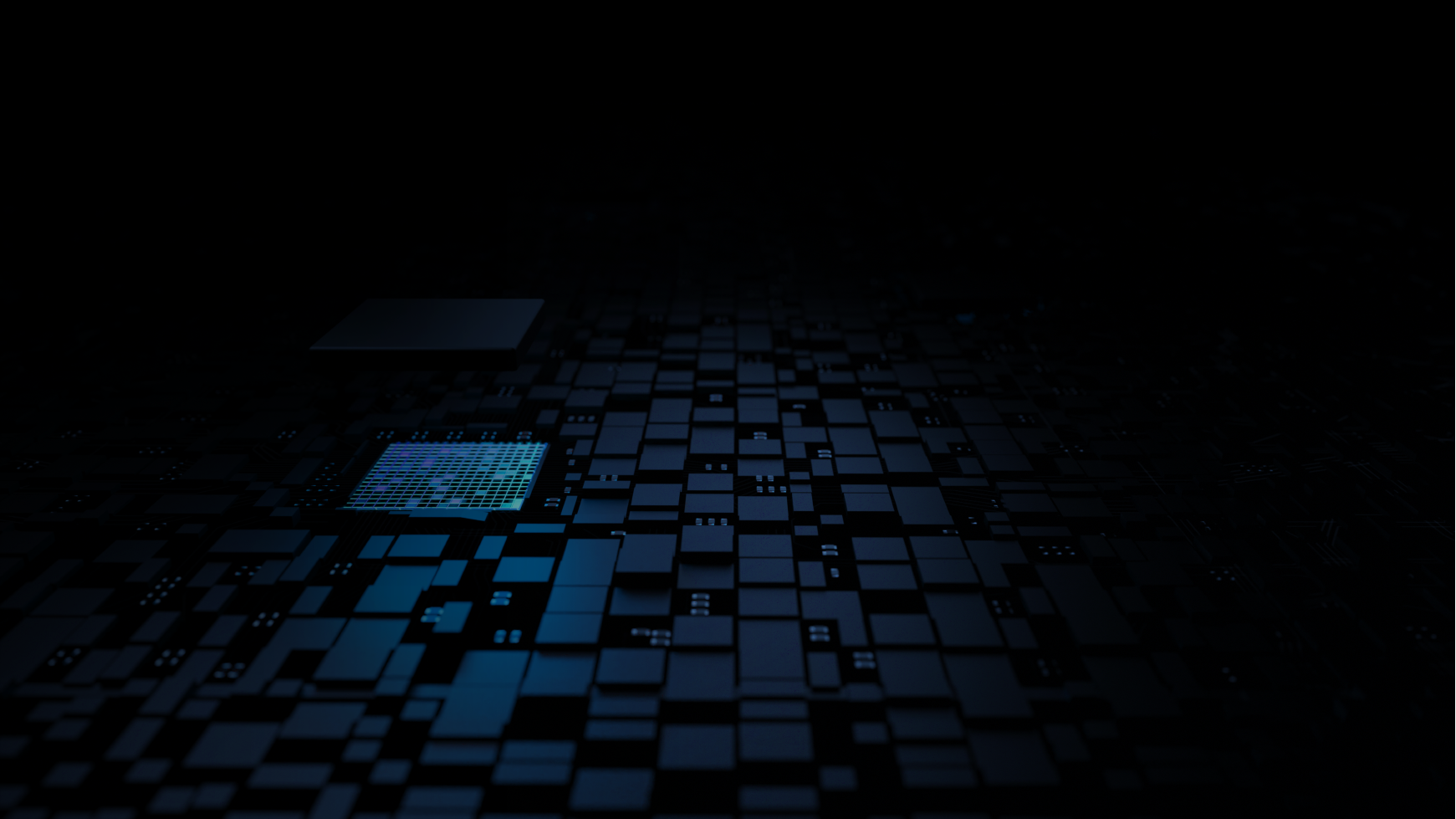
What is AMCOSTAR?
Amcostar is a Eurostars/Eureka and Innovation Fund Denmark funded, international collaboration between Dacoma, Automasjon & Data, Tuco and the University of Southern Denmark / SDU Mechatronics. Each partner brings in unique know-how and experience.
Together, we will develop and demonstrate an integrated Airkeel and adaptive control system (ACS) enabling enhanced stability and capacity for smaller boats (6-40m). The Airkeel is a novel stabilizer, based on an air filled flotation body that is mounted to the bottom of the keel of the vessel.
The Airkeel can be swung in a pendulum motion from side to side, stabilizing the vessel against the heel and roll motions. The added buoyancy leads to lighter, more stable boats with higher load & crane capacity to size ratio. At the same time ship resistance is decreased at semiplaning speeds which reduces fuel consumption by 5-10%.
Applying advanced learning/AI with new data derived, will permit comfortable and safe operations in all weather, at all speeds, even at zero speed.
The main goal of the project is to demonstrate safer, more comfortable and more fuel efficient work - and crewboats for all season operation.
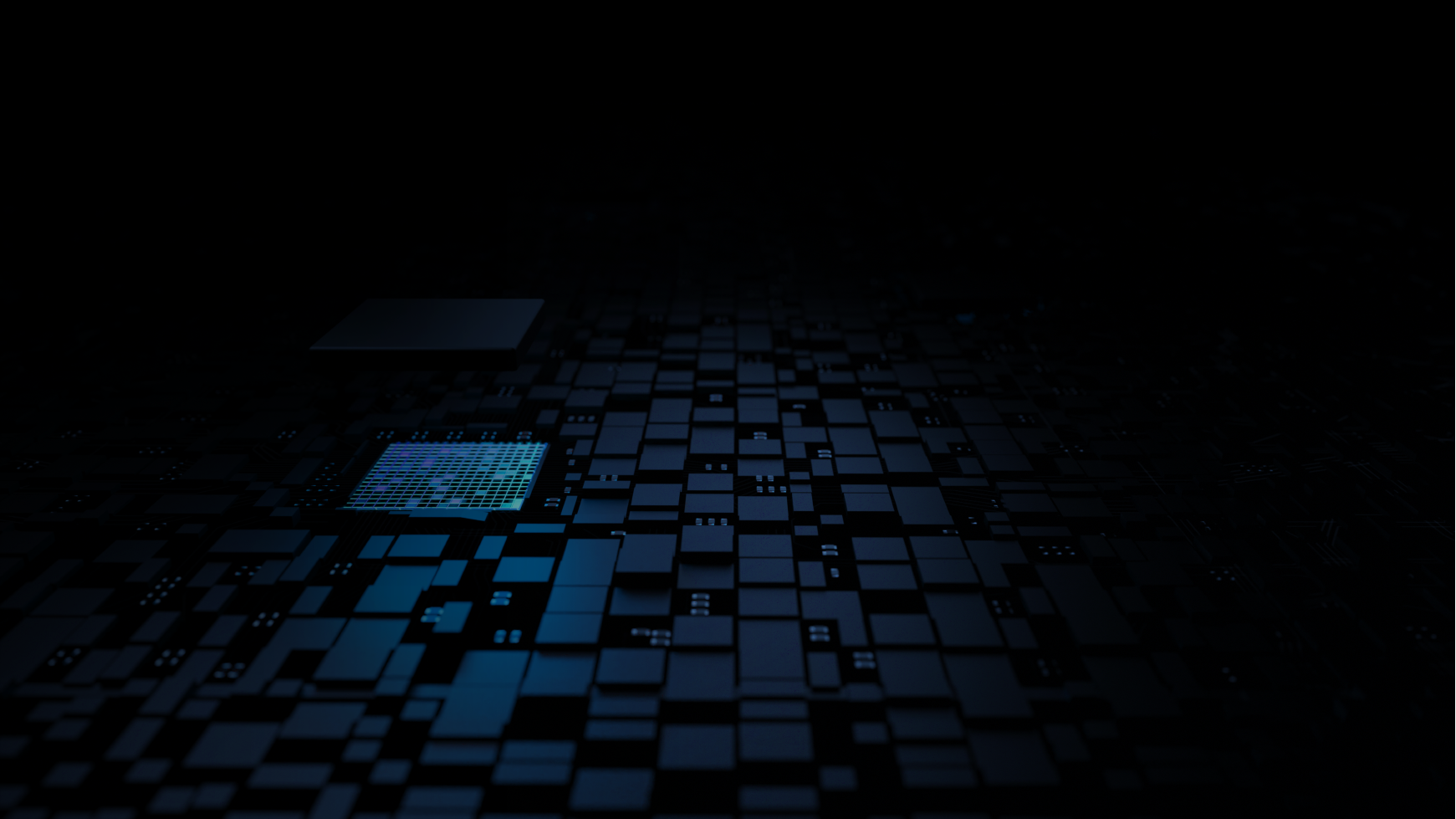
How are we going to achieve this?
1. Assessment of control system requirements by data collection
Our promise to the market is to develop optimum stabilizer solutions for all customer applications.
In order to achieve this, we need to understand even the most challenging use case in detail.
Customer interviews, experiences from ship designers and shipbuilders, both among the project partners and from external sources, and ship motion data will thoroughly be analyzed.
The results from this initial study will be used as the launch pad for understanding and defining the uses case dependent specification requirements. Those again serves as input for simulations, modelling and the conceptual design phase where we are going to design the hardware and the software for the most prominent use cases.
2. Optimization, test and validation of the ACS
In the next phase, we will mount an ACS optimized Airkeel on a ProZero work-/crewboat for testing, optimization, and validation of uses cases.
We will focus on the special requirements to be met in market segments as e.g.within aquaculture, fast work-/and crewboats for offshore constructions, crew transfer to and from offshore wind farms, coast guard, patrolling, pilot and SAR applications. In detail, we will benchmark and validate enhanced comfort and safety in all weather and at all speeds, increased crane and load capacity, as well as improved fuel efficiency. The aim is to develop a stable and comfortable platform to work from for all hard working people at sea.
3. Improvement and further development of business cases
A large fraction of our work in the project is devoted to improving the existing business cases and to co-develop new ones. Early customer involvement and continuous dialogues with other stakeholder involvement will make sure that feedback on our product and new trends are being captured and are becoming and integral part of our development. If necessary, the ACS design will be adjusted and validated against the benchmarks and requirements from our customers.
No rockin’ no rollin’ – that is our mission.
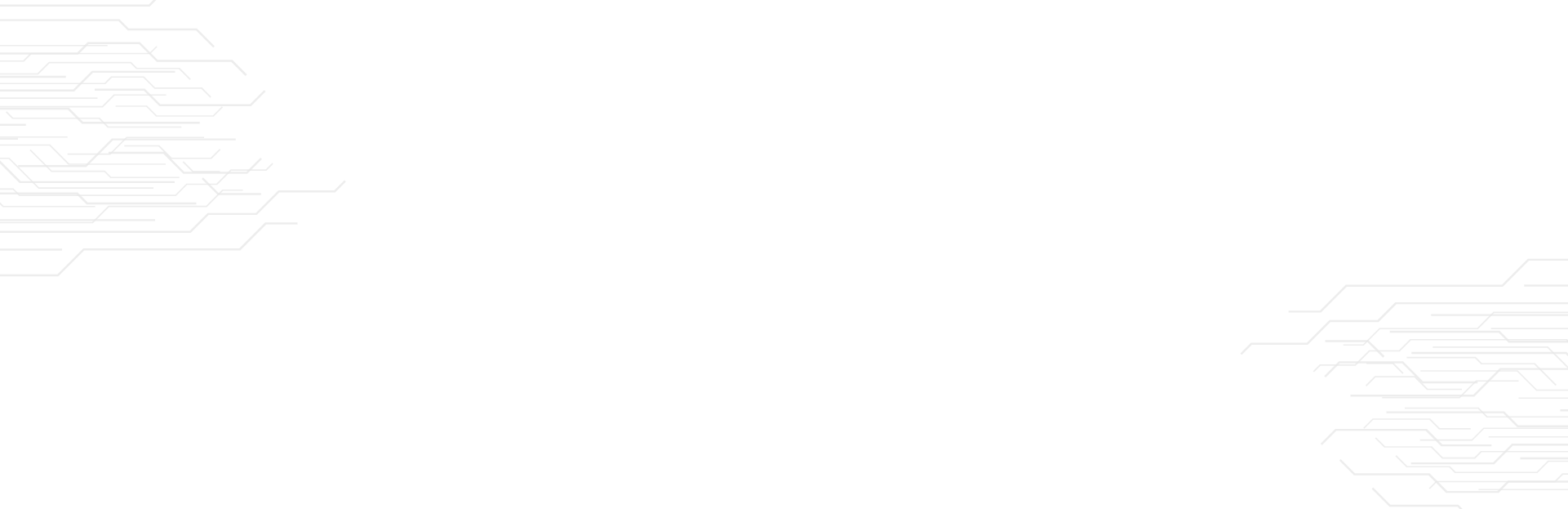
Project milestones
The major milestones of the 24 months project ending in July 2023 are:
Demonstration and validation of Airkeel stabilisers within crew transfer.
Improving comfort and safety with adaptive control.
Extending ProZero boat
a) crane and load capacity
b) weather
Validation through motion data
Fuel consumption and carbon footprint reduction
Get to know the consortium partners
Visit the column on the right and learn how the different consortium partners contributes with their expertise to the AMCOSTAR project.
-
Stabilizer development & delivery
Software development of the control systems
Feasibility tests
Full scale tests
Dissemination
Customer demos
-
Boatbuilding and boat design expertise
Aquaculture custom-tailored boat
Motion data supported workboat design and fleet optimization
Integration design of Airkeel stabilizer demo boat
Dissemination, customer demos
-
Input to specification requirements/ benchmarking.
Boat motion data taking, simulations or towing tank experiments.
Seasickness monitoring and analysis.
Test system implementation.
Dissemination.
-
Control system theory.
Modelling and simulations.
Algorithms, optimisation and validation of adaptive control.
Data analysis, evaluation.
Scientific publications.
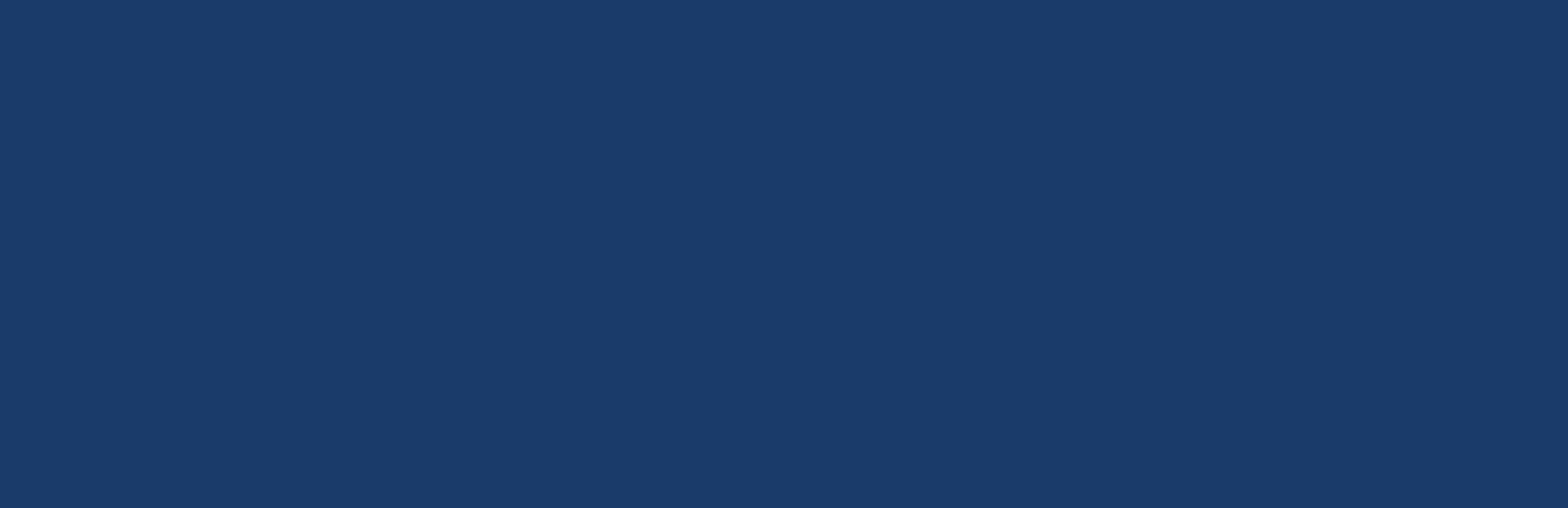

Dacoma
DACOMA is a Danish maritime start-up that designs, manufactures, and delivers innovative wave stabilizer solutions for crew transfer vessels and crew-/workboats. Our product targets the market segments of offshore wind installations, services and operations, aquaculture, offshore constructions, coast-guard and rescue services, small passenger vessels like water busses, super yachts, leisure and tourist boats.
Our goal is to increase productivity of service and installation personnel due to eliminating motion sickness, to make crew transfer safer. Another unique property of our stabilizer is that vessel utilization is increased due to improved seakeeping and due to doubling the workboat load and crane capacity. In addition, our solution saves fuel, is more compact than competing systems and works in a wide speed range.
Dacoma’s vessel stabilizer is based on our own, patented Airkeel technology that we have developed in-house, including our control system, which is the key component.
The DACOMA team has been working on bringing modern machine learning to small work boats to help with seasickness and hence increase the efficiency of wind farm technicians, who are not trained mariners. While working on this challenge we realized the potential in increasing stability of small work boats in static operation environments. In short, increased stability will improve the efficiency of the operations and the well-being of the crew.
We constantly optimize the mechanics and electrical components of the drive system and the hydrodynamics of the underwater appendages to the benefit of our customers. However, the biggest leap towards more comfort & safety and increased operational flexibility for different crane and load scenarios under all thinkable weather conditions, will come from collecting ship motion data and using them to “train” the adaptive control system (ACS) that we are going to develop in this project. The ACS will hence be the key component of our stabilizer system for many years from now.
One of the major advantages of the ACS over our existing control system will be that the efforts of control system tuning during installation of our stabilizer into different boat types (refits or newbuilds) will be reduced to basically one day. This optimizes costs, shortens delivery times and increases adherence to delivery. Our stabilizer will not only out-perform existing stabilizer systems, but also will be easy and fast to be integrated.
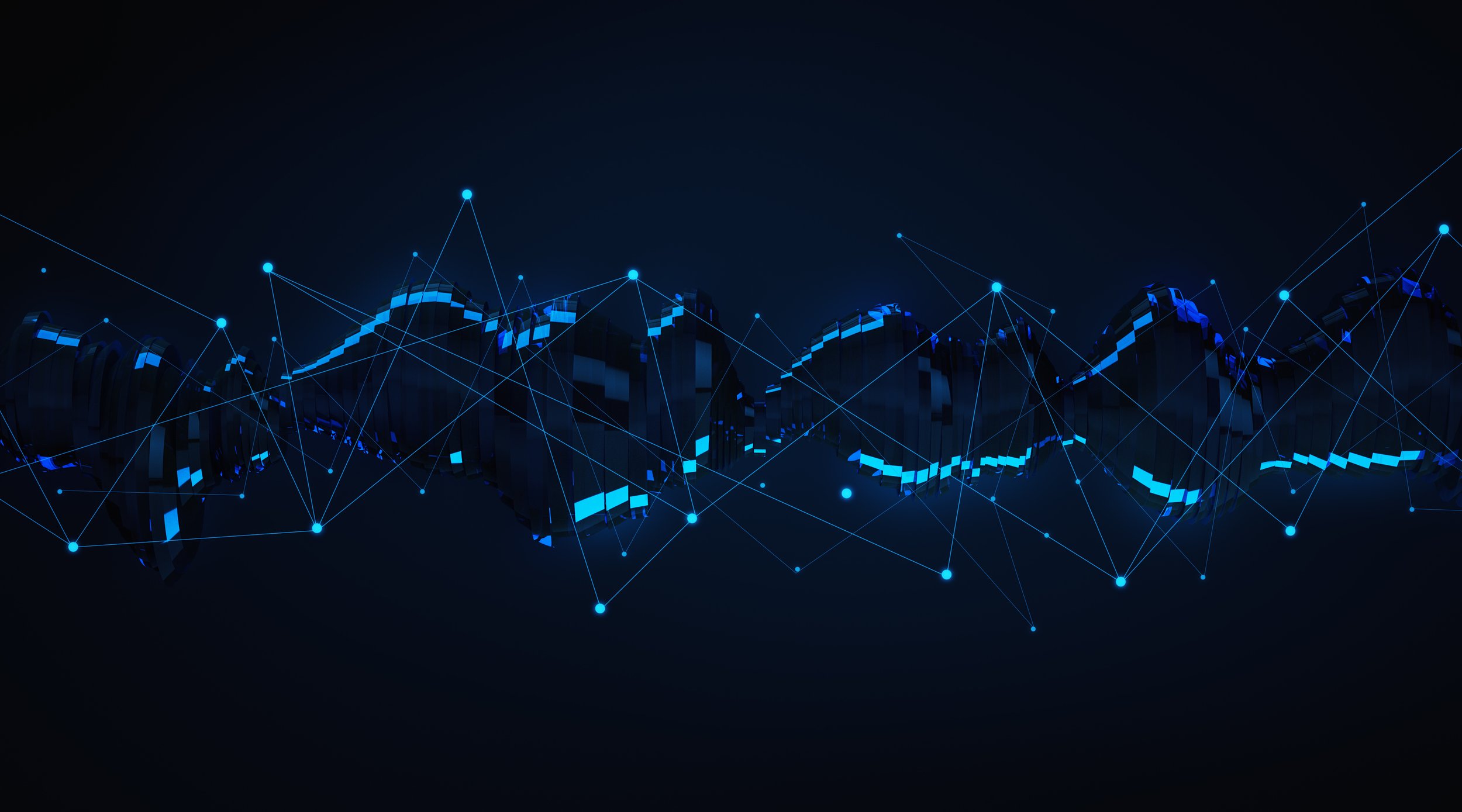
Tuco
Tuco Marine Group is the parent company and Tuco Yacht Yard and Tuco Composites are the two subsidiary companies. The production team at Tuco is a highly skilled and experienced team of boat builders, composites experts and carpenters. We specialize in light structures and hulls manufactured with composite materials such as carbon fibre. Tuco supplies a range of different composite structures for the shipping industry and other industries where low weight and strength are important factors.
Tuco Yacht Yard offers custom-built ships, repairs, maintains the vessels and performs all kinds of different jobs related to composite materials. We have evolved to be a stakeholder in developing the industry towards more environmentally sustainable vessels.
The Tuco team has been working to produce lighter and stronger workboats for professional users to contribute to environmentally sustainable vessels industry since 2000. We are well positioned to re-invent the work boat building towards a future.
By increasing the stability of small work boats, the operations performed by our customers can be finalized in shorter periods of time thanks to the increased computed precision. Improved boat stability will further increase the operation window, by for example increasing the measured amplitude of the waves, which the user can operate in. With these aspects, the Amcostar project has the potential to contribute to decreasing the carbon footprint of salmon industry and any other application from which the user benefits from an increased stability of the workboat.
Tuco has been a front runner in revolutionizing the boat production and making it more environmentally friendly, increasing productivity and last but not least safety and comfort of the workers onboard. We deem this project aligns with our company mission and vision.
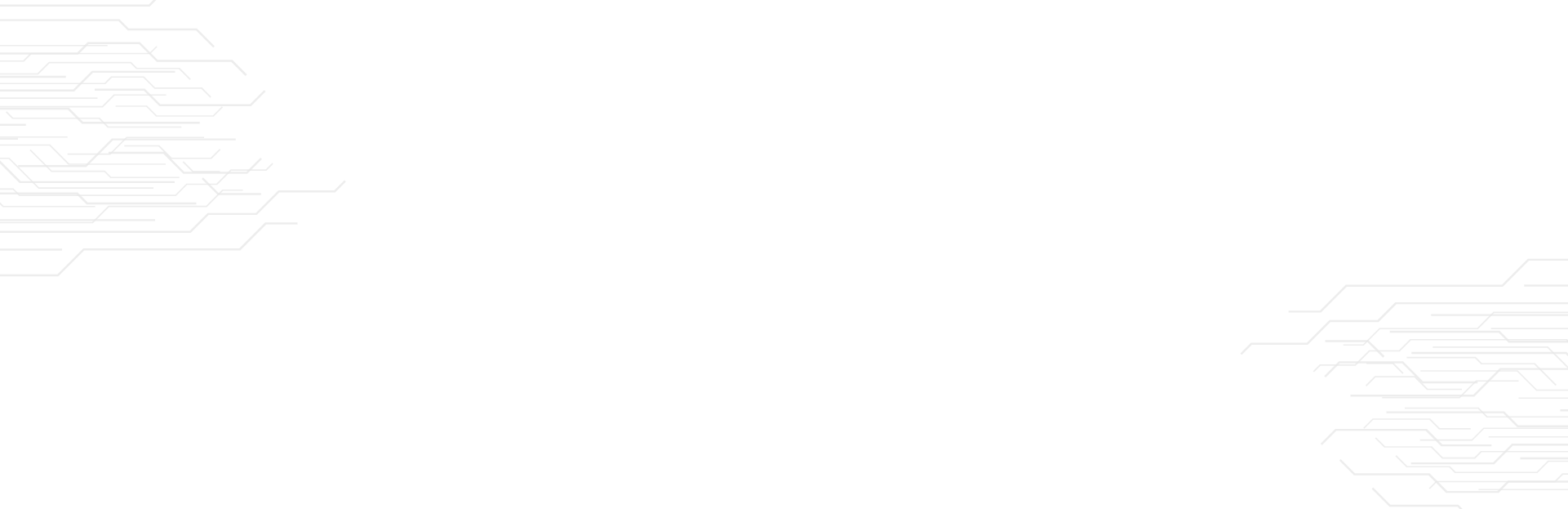
Wise Group/ Automasjon & Data
Automasjon & Data AS (A+D) was established in 1991 as a software house and has since then developed into one of the world’s leading companies for MetOcean or meteorological and oceanographic data systems.
The main products range from simple Weather Stations to advanced complete Helideck Monitoring Systems and Environmental Monitoring Systems for marine and offshore users and other demanding applications. Such systems are measuring wind, temperatures, barometric pressure, motions, sea currents, waves, and more. They include a number of additional sensors and tailor-made functions that are essential for offshore users.
Typical add-on functions can be Anchor Line Monitoring, Stress Monitoring, Motion and Accelerations measurements, Alarm functions, SCADA applications etc.
All off-shore platforms and vessels need environmental data for daily operational use and as an important tool for safety purposes. In the later years these systems are also being tailor-made to measure the movements and conditions of the helideck and are used as a tool for improving the safety for helicopter traffic.
A+D have a lot of valuable experience from many different applications and a large number of special functions that have been integrated into our software in order to improve the user interface. Special emphasize has been put upon making the data displays easily understandable for non-technical users.
Our aim is to become the world leader in vessel motion monitoring systems (VMMS) and hence the technology and business developments we will gain during the AMCOSTAR project are crucial. We have always aimed at being a front-runner in technology development, and we see this project as a ground-breaking technology in vessel stabilization optimization.
We are also very invested in increasing the crew well-being, and this project will enable us to gather deep insights into comfort and safety indicators.
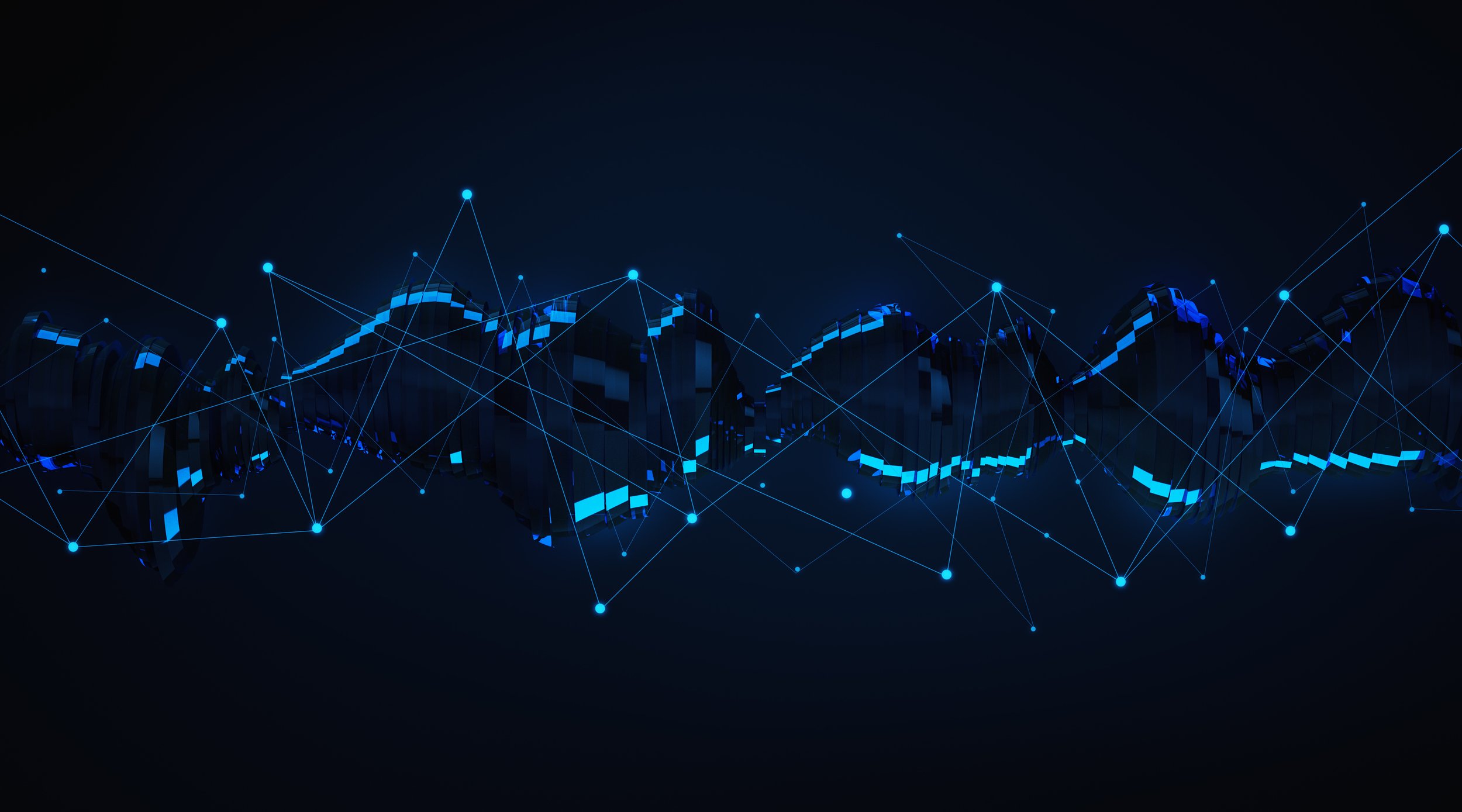
SDU Mechatronics
The Department of Mechanical and Electrical Engineering (IME) at the University of Southern Denmark (SDU Mechatronics) was established to strengthen the existing specialist fields within Mechanics, Mechatronics and Electronics. With a focus on sustainability and industrial collaboration, the department is training engineers at both BEng, BSc and MSc level in mechanical engineering, mechatronics, design engineering and electronics.
The SDU Mechatronics/IME team have tackled many different control and estimation techniques throughout their career, with nonlinear control, backstepping, neural networks-based control, optimal and adaptive control, model-predictive control, nonlinear observers, the modulating function method to name but a few.
We apply these control algorithms experimentally on a wide number of different platforms and embedded computers that are widely used in the industry. In doing so, the important issue of rapid prototyping control systems comes into play. The team also have decades of expertise in this area (Matlab/Simulnk, S-Functions, real-time capabilities and deployment), including knowledge and expertise from maritime projects.
SDU Mechatronics will benefit through research opportunities, data acquisitions, applied learnings, student collaboration opportunities and not least publications from the Amcostar project. As part of Amcostar, we can continue and expand the research and development activities within wave stabilization and vessel motion monitoring to provide knowledge on sustainability in marine industry and increase its industry collaboration. Additionally, the project offers the possibility to extend our prototyping control systems experience and know-how to help marine industry to increase its efficiency which is central to contribute to sustainability in aquaculture.
The very close cooperation with industry in this project is of great attraction to our department and we foresee long-term involvement with AMCOSTAR project partners.
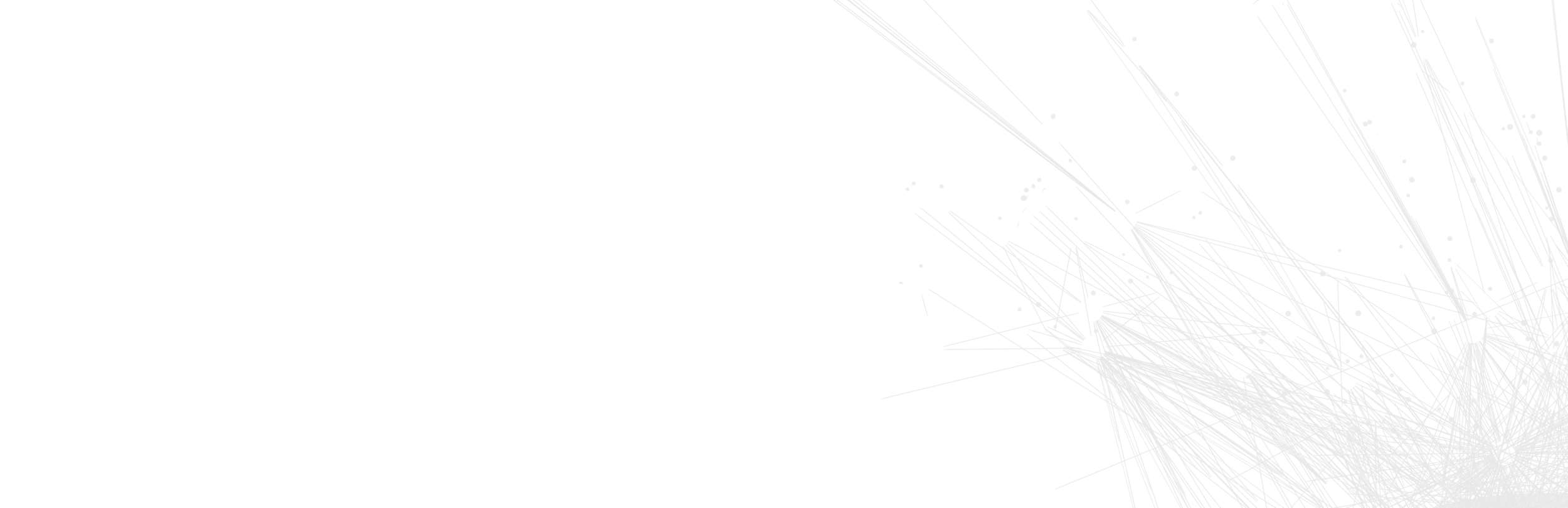
Partner Testimonials
“We are enthusiastic about AMCOSTAR, because we can build on decades of experience in adaptive control systems and create new methods and algorithms for the most advanced control within the field.”
— Hossein Ramezani, University of Southern Denmark / SDU Mechatronics.
The project fits perfectly with our strategy. We can attract brilliant students and have some highly visible publications out of it”
— Jerome Jouffroy , University of Southern Denmark / SDU Mechatronics.
“A lot of our ProZero work- and crewboat customers will benefit from an even more safe and stable platform to work from.”
“I’m eager to see how much additional crane and load capacity can be added to our workboats in order to increase their operational range and to have verified other eventual impacts to the performance of our boats.”
— Jonas Pedersen, CEO, Tuco
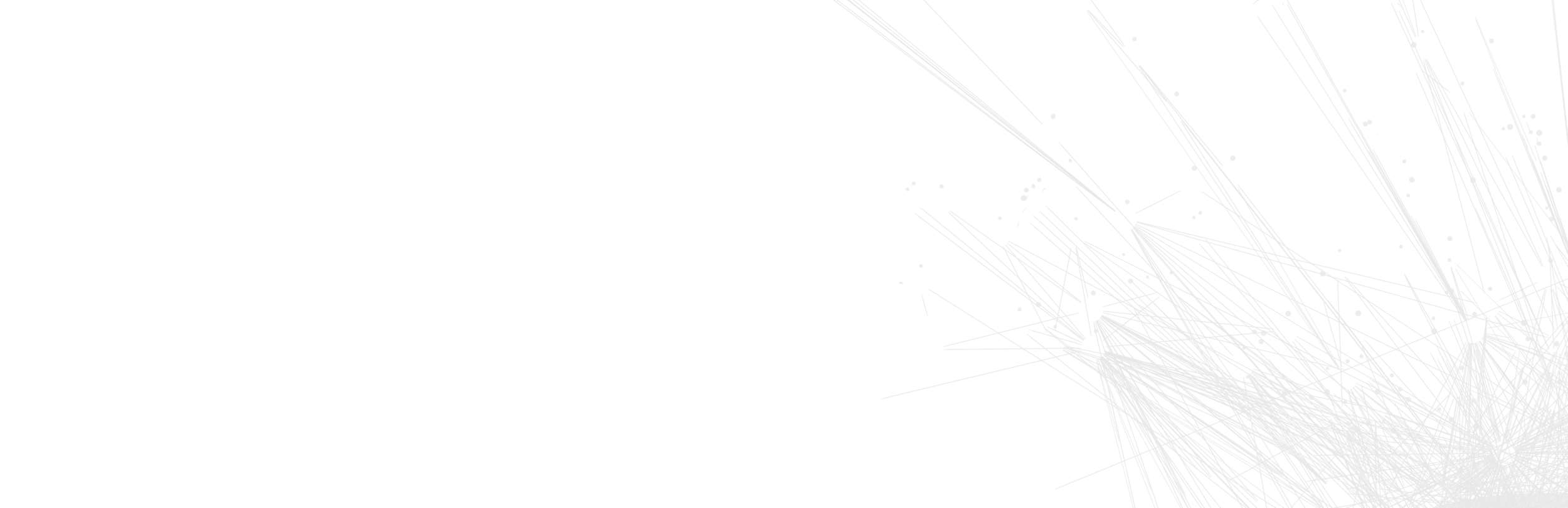
“We know from previous studies that motion sickness and bad weather cost our customers a lot. We hope to combine our meteorological tools with the new adaptive control technology to develop new products for a wider range of workboat and crew transfer vessel customers.”
— Jon Arne Silgjerd, Automasjon & Data AS.
“The project is a fantastic opportunity to get faster to the market with our Airkeel stabilizer. It simply boosts the launch of our product in all segments of workboats, because AMCOSTAR not only makes the boats perform better under awkward weather conditions, but also makes them operational more flexible.”
— Arnd Baurichter, Dacoma.
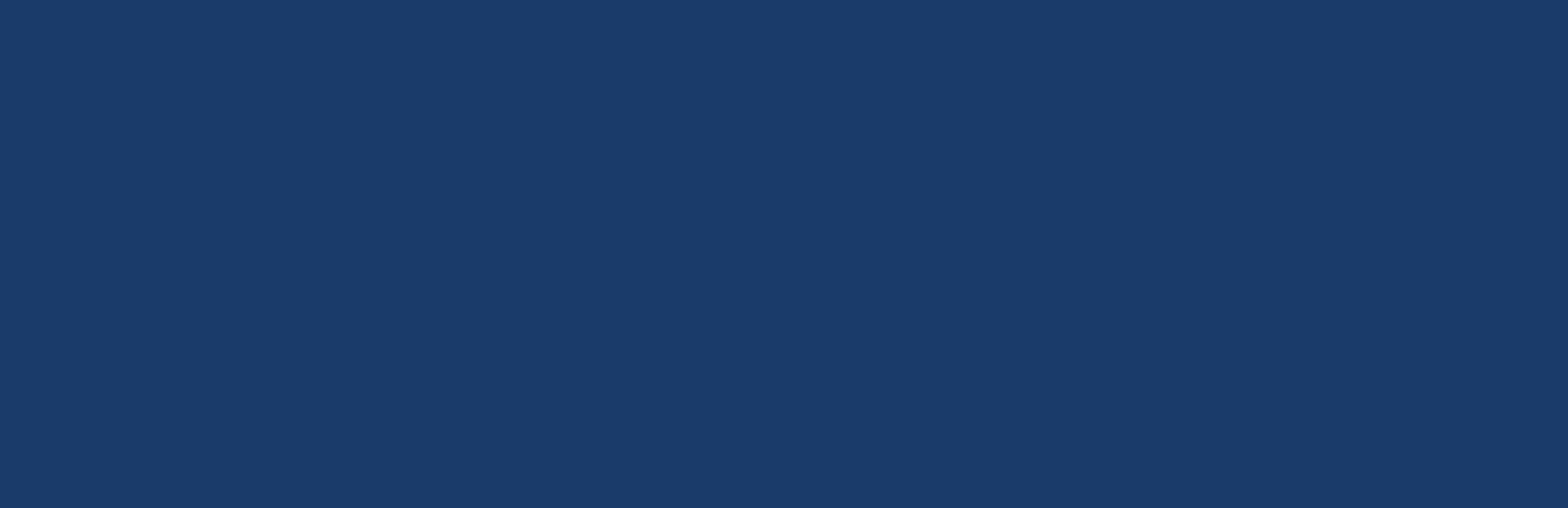